మీరు అండర్ఫ్లోలో ఎక్కువ నీరు మరియు ఓవర్ఫ్లోలో ఘనపదార్థాలతో ఇబ్బంది పడుతున్నారా? పదేపదే సాంద్రత కొలత మరియు మానవ తప్పిదాలను తొలగించడం ద్వారా చిక్కగా చేసే ఆపరేషన్ను ఆప్టిమైజ్ చేయాలనుకుంటున్నారా? నీటిని ఆదా చేయడానికి మరియు ప్రాసెసింగ్ కోసం విలువైన పదార్థాన్ని సేకరించడానికి చాలా మంది తుది వినియోగదారులు ఖనిజ ప్రాసెసింగ్ పరిశ్రమలో అదే సమస్యలను ఎదుర్కొంటున్నారు. ఈ లక్ష్యాలను చేరుకోవడంలో రియల్-టైమ్ డెన్సిటీ మీటర్ సమర్థవంతంగా పనిచేస్తుంది.
కింది వ్యాసం థిక్నర్ ట్యాంకుల యొక్క వివిధ పాయింట్ల వద్ద సాంద్రత నియంత్రణ యొక్క ప్రయోజనాలు మరియు ప్రయోజనాలను వివరించడంపై దృష్టి పెడుతుంది. గట్టిపడటం ప్రక్రియకు సంక్షిప్త పరిచయంతో ప్రారంభిద్దాం, తరువాత విభజన ప్రక్రియలో సాంద్రతను కొలవడానికి ఐదు కారణాలను చూద్దాం.
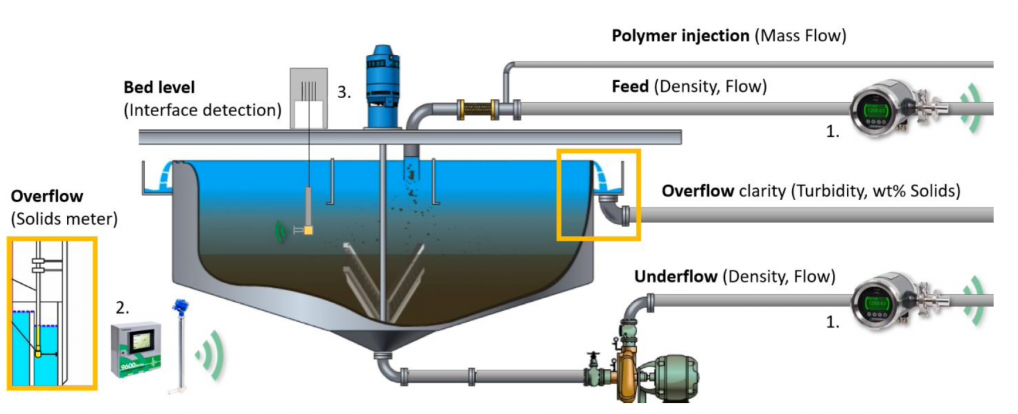
గట్టిపడటం యొక్క విధి ఏమిటి?
గట్టిపడే ప్రక్రియలో ఘన-ద్రవ మిశ్రమాన్ని దట్టమైన అండర్ఫ్లోగా మరియు స్పష్టమైన ఓవర్ఫ్లోగా వేరు చేయడం జరుగుతుంది. మొదటిది ఘన కణాలను కలిగి ఉంటుంది మరియు తరువాతిది సాధ్యమైనంతవరకు మలినాలను తొలగిస్తుంది. విభజన ప్రక్రియ గురుత్వాకర్షణ ఫలితం. వివిధ పరిమాణాలు మరియు సాంద్రతలలో ఉన్న అన్ని కణాలు ట్యాంక్ ద్వారా వేర్వేరు పొరలను ఏర్పరుస్తాయి.
గాఢతలు మరియు టైలింగ్లను వేరు చేయడానికి ఖనిజ ప్రాసెసింగ్లోని అవక్షేపణ ట్యాంక్లో గట్టిపడటం ప్రక్రియలు జరుగుతాయి.
గట్టిపడటంలో అవసరమైన కొలత పాయింట్లు
ఆన్లైన్ ద్రవ సాంద్రత మీటర్లుథికెనర్ల పనితీరును ఆప్టిమైజ్ చేయడానికి అవసరం. ఉదాహరణకు, ఇన్స్టాలేషన్ పాయింట్లలో థికెనర్ ట్యాంక్ యొక్క ఫీడ్, అండర్ఫ్లో, ఓవర్ఫ్లో మరియు ఇంటీరియర్ ఉన్నాయి. పైన పేర్కొన్న పరిస్థితులలో, ఈ సెన్సార్లనుస్లర్రీ సాంద్రత మీటర్లేదాబురద సాంద్రత మీటర్. డ్రైవ్లు, పంపుల ఆటోమేటిక్ నియంత్రణను మెరుగుపరచడంలో మరియు ఫ్లోక్యులెంట్ల సమర్థవంతమైన మోతాదుకు కూడా ఇవి సహాయపడతాయి.
సాంద్రతను కొలవడానికి కారణాలు
సాంద్రత కొలతకు కారణాలు ఒక్కొక్కటిగా మారవచ్చు. పారిశ్రామిక ఆప్టిమైజేషన్ కోసం సాంద్రత పర్యవేక్షణ యొక్క ప్రాముఖ్యతను ఈ క్రింది ఐదు పరిస్థితులు హైలైట్ చేస్తాయి.
నం. 1 నీటి పునరుద్ధరణ
మైనింగ్ మరియు ఖనిజ పరిశ్రమలలో నీటిని అత్యంత ముఖ్యమైన ఆస్తులలో ఒకటిగా పరిగణిస్తారు. అందువల్ల, నీటిని తిరిగి పొందడం లేదా నీటి పునర్వినియోగం గట్టిపడటం ఖర్చును బాగా ఆదా చేస్తుంది. అండర్ఫ్లో సాంద్రతలో 1-2% చిన్న పెరుగుదల అంటే ఆపరేటింగ్ ఇన్స్టాలేషన్లకు పెద్ద మొత్తంలో నీరు అవసరం. టెయిలింగ్ డ్యామ్లలో దృఢత్వాన్ని నిర్ధారించడంలో సాంద్రత పెరుగుదల ప్రభావవంతంగా పనిచేస్తుంది, ఆనకట్టలకు ఎక్కువ ద్రవం పంప్ చేయబడితే అవి కూలిపోవచ్చు.
నం. 2 మినరల్ రికవరీ
కాన్సంట్రేట్ థికెనర్లలో, ఫీడ్ సాధారణంగా ఫ్లోటేషన్ సర్క్యూట్ నుండి ఉద్భవించింది. ఫ్లోటేషన్ అంటే గురుత్వాకర్షణ ద్వారా కణాలను వేరు చేయడం. మరో మాటలో చెప్పాలంటే, గాలి బుడగలు జతచేయబడినవి ఉపరితలం పైకి లేచి తొలగించబడతాయి, మరికొన్ని ద్రవ దశలోనే ఉంటాయి. ఉత్పత్తి థికెనర్లో ఈ ప్రక్రియ జరిగినప్పుడు, నురుగు ఘనపదార్థాలను ఓవర్ఫ్లోలోకి తీసుకువెళుతుంది.
ఈ ఘనపదార్థాలు విలువైనవి మరియు తిరిగి పొందకపోతే, సాంద్రీకృత లోహం యొక్క మొత్తం రికవరీ రేటును తగ్గించవచ్చు. అదనంగా, ఓవర్ఫ్లోలోని ఘనపదార్థాలు అధిక రియాజెంట్ ఖర్చులకు, పంపులు మరియు వాల్వ్లకు నష్టానికి మరియు నిర్వహణ ఖర్చులను పెంచడానికి దారితీయవచ్చు, ఉదాహరణకు ఘనపదార్థాలు పేరుకుపోయినప్పుడు నీటి ట్యాంకులను శుభ్రపరచడం వంటివి.
ఓవర్ఫ్లోలో కోల్పోయిన ఘనపదార్థాలలో దాదాపు 90% చివరికి ప్రక్రియ యొక్క తరువాతి దశలలో (ఉదాహరణకు, ట్యాంకులు మరియు ఆనకట్టలలో) తిరిగి పొందబడతాయి. అయితే, మిగిలిన 10%, ఇది గణనీయమైన ఆర్థిక విలువను సూచిస్తుంది, ఇది శాశ్వతంగా కోల్పోతుంది. కాబట్టి ఓవర్ఫ్లోలో ఘనపదార్థాల నష్టాన్ని తగ్గించడం ప్రాధాన్యతగా ఉండాలి. ప్రక్రియ నియంత్రణ సాంకేతికతలలో పెట్టుబడి పెట్టడం వల్ల రికవరీ రేట్లు పెరుగుతాయి మరియు పెట్టుబడిపై త్వరిత రాబడిని అందించవచ్చు.
లాన్మీటర్ వాడకంసాంద్రత మీటర్లుమరియుఫ్లో మీటర్లుఅండర్ఫ్లోలో చిక్కగా చేసే పనితీరును బాగా పర్యవేక్షించడానికి వీలు కల్పిస్తుంది. సాంద్రత లేదా ఘనపదార్థాల మీటర్లతో ఓవర్ఫ్లోలోని ఘనపదార్థాలను నిజ-సమయంలో గుర్తించడం కూడా సాధ్యమవుతుంది. ప్రత్యక్ష ప్రక్రియ ఆప్టిమైజేషన్ కోసం పరికరాల 4-20mA సంకేతాలను నియంత్రణ వ్యవస్థలో అనుసంధానించవచ్చు.
3 సమర్థవంతమైన ఫ్లోక్యులెంట్ ఉపయోగం
ఫ్లోక్యులెంట్లు అవక్షేపణ సామర్థ్యాన్ని మెరుగుపరచడంలో పనిచేస్తాయి, అవి ద్రవాలలోని కణాలు కలిసిపోవడానికి దోహదపడే రసాయనాలు. ఫ్లోక్యులెంట్ల మోతాదు రియాజెంట్ మరియు కార్యాచరణ సామర్థ్యంపై ఖర్చు నియంత్రణను పరిగణిస్తుంది. సాంద్రత మీటర్ గట్టిపడే ఫీడ్ కోసం ఖచ్చితమైన మరియు నమ్మదగిన సాంద్రత నియంత్రణను అనుమతిస్తుంది. స్వేచ్ఛా కణ స్థిరపడటానికి అనుమతిస్తూనే ఫీడ్ స్లర్రీలో బరువు ద్వారా సాధ్యమైనంత ఎక్కువ ఘనపదార్థ శాతాన్ని సాధించడం లక్ష్యం. ఫీడ్ స్లర్రీ సాంద్రత లక్ష్యాన్ని మించి ఉంటే, అదనపు ప్రక్రియ మద్యం జోడించాలి మరియు తగినంత ఫీడ్ వెల్ మిక్సింగ్ ఉండేలా చూసుకోవడానికి మరింత మిక్సింగ్ శక్తి అవసరం కావచ్చు.
ఇన్లైన్ డెన్సిటీ మీటర్ని ఉపయోగించి ఫీడ్ స్లర్రీ యొక్క రియల్-టైమ్ డెన్సిటీ కొలత ప్రక్రియ నియంత్రణకు చాలా ముఖ్యమైనది. ఇది సమర్థవంతమైన ఫ్లోక్యులెంట్ వినియోగాన్ని నిర్ధారిస్తుంది మరియు మిక్సింగ్ ప్రక్రియను ఆప్టిమైజ్ చేస్తుంది, థికెనర్ దాని లక్ష్య పరిధిలో పనిచేస్తూనే ఉంటుంది.
4 ఫ్లోక్యులేషన్ సమస్యలను వెంటనే గుర్తించడం
ఆపరేటర్లు థికెనర్లలో స్థిరమైన పరిస్థితులను నిర్వహించడానికి ప్రయత్నిస్తారు, కనిష్ట ఘనపదార్థాలతో స్పష్టమైన ఓవర్ఫ్లోను మరియు కనిష్ట ద్రవంతో దట్టమైన అండర్ఫ్లోను సాధిస్తారు. అయితే, ప్రక్రియ పరిస్థితులు కాలక్రమేణా మారవచ్చు, ఇది పేలవమైన స్థిరపడటానికి, తగ్గిన అండర్ఫ్లో సాంద్రతకు మరియు ఓవర్ఫ్లోలో అధిక ఘనపదార్థాలకు దారితీస్తుంది. ఈ సమస్యలు ఫ్లోక్యులేషన్ సమస్యలు, ట్యాంక్లో గాలి లేదా నురుగు లేదా ఫీడ్లో అధికంగా అధిక ఘనపదార్థాల సాంద్రత నుండి ఉత్పన్నమవుతాయి.
ఇన్స్ట్రుమెంటేషన్ మరియు ఆటోమేషన్ ఆపరేటర్లు అటువంటి సమస్యలను నిజ సమయంలో గుర్తించడం ద్వారా నియంత్రణను నిర్వహించడానికి సహాయపడతాయి. ఇన్లైన్ కొలతలకు మించి, అల్ట్రాసోనిక్ బెడ్ లెవల్ ప్రోబ్స్ వంటి ట్యాంక్ ఆధారిత ఇన్స్ట్రుమెంటేషన్ కీలకమైన అంతర్దృష్టులను అందించగలదు. ఈ “డైవర్” ప్రోబ్స్ ట్యాంక్ లోపల పైకి క్రిందికి కదులుతాయి, మట్టి స్థాయిలను, స్థిరపడే మండలాలను మరియు ఓవర్ఫ్లో స్పష్టతను ప్రొఫైలింగ్ చేస్తాయి. బెడ్ లెవల్ కొలతలు ఫ్లోక్యులేషన్ నియంత్రణ వ్యూహాలకు ప్రత్యేకంగా ఉపయోగపడతాయి, స్థిరమైన పనితీరును నిర్ధారిస్తాయి.
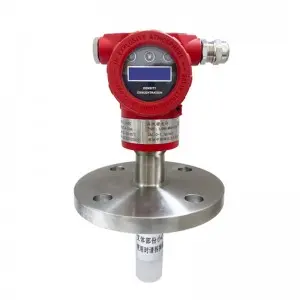
స్లర్రీ డెన్సిటీ మీటర్ (SDM)
స్లర్రీ డెన్సిటీ మీటర్ (SDM) అనేది సాంప్రదాయ న్యూక్లియర్ డెన్సిటీ మీటర్లకు పర్యావరణ అనుకూల ప్రత్యామ్నాయం. ఇది ప్రపంచవ్యాప్తంగా వందలాది ఇన్స్టాలేషన్లతో వేగంగా ప్రజాదరణ పొందింది. SDM ఖచ్చితమైన మరియు నమ్మదగిన సాంద్రత కొలతలను అందిస్తుంది, ఇది ఆధునిక ఖనిజ ప్రాసెసింగ్ ప్లాంట్లకు ఆదర్శవంతమైన పరిష్కారంగా మారుతుంది.
సాంద్రతను కొలవడం అనేది చిక్కగా చేసే సామర్థ్యాన్ని మెరుగుపరచడంలో కీలక పాత్ర పోషిస్తుంది మరియు ప్రక్రియ నియంత్రణకు కీలక పనితీరు సూచికగా పనిచేస్తుంది. అధునాతన కొలత సాంకేతికతలు మరియు ప్రక్రియ నియంత్రణ వ్యూహాలను అవలంబించడం ద్వారా, ఆపరేటర్లు చిక్కగా చేసే పనితీరును ఆప్టిమైజ్ చేయవచ్చు, రికవరీ రేట్లను మెరుగుపరచవచ్చు మరియు కార్యాచరణ ఖర్చులను తగ్గించవచ్చు.
పోస్ట్ సమయం: డిసెంబర్-30-2024